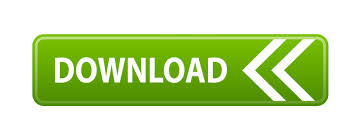
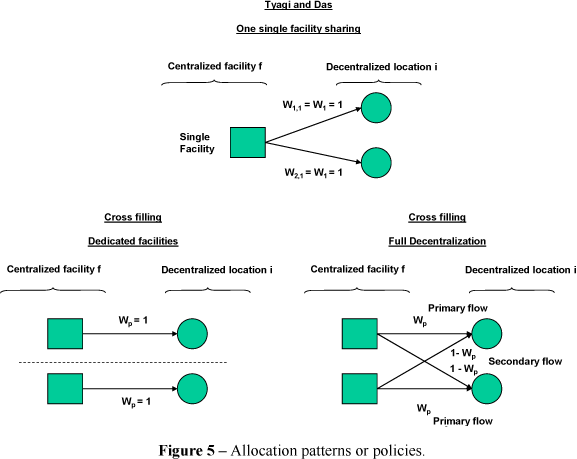
A day less in transport equals a day less inventory in your pipeline. Any transportation reduction also creates an additional direct reduction of transit stock. A 25% lead time reduction equals a 13% safety stock reduction. If you carry safety stock, the reduction will be the square root of reduced time. Shorter and less variable lead times require less inventory. For transportation time: use faster modes of transport or relieve bottlenecks at shipping/receiving. Possible solutions include: advance notice of upcoming needs, a longer-range forecast, and fixed cycle replenishment. Can you work with your suppliers to help them reduce their lead times? Understand their constraints. Generally, the review time is longer than the manufacturing time. The manufacturing time includes a review period for your supplier on top the actual manufacturing time. Can this minimum be reduced so the order can be sent sooner? Find out how long, and how variable, these three components are.Īre there any ways to reduce the review period? Must you wait until the end of the month to place an order? Long review periods may be driven by system limitations can these limitations be overcome? Can weekly cycles be reduced to daily? Frequently, a supplier will have minimum order requirements that forces batching of many products with replenishment needs. The transportation time is the time it takes from availability to ship until the material is received and available for use at the next location. The manufacturing time is the time from when the order is sent until product is available to ship. The review period is the time from when the need is identified to when the order is sent upstream.

Break this lead time into three components: the review period, manufacturing time and transportation time. This can be important for raw material lead time or lead times between your internal tiers of distribution. Number 2: Reduce replenishment lead times After gathering this information, you have the makings of a supply chain data warehouse for further analysis. These charts are an excellent way to begin looking at your inventory. Again, do your A inventory items represent at least 50% of your sales? If not, inventory may be out of balance. A significant amount of inventory on low demand items may indicate problems with product run-outs, transitions, engineering change management, and managing obsolete inventory.įor the second chart, classify your items based on inventory. Do your A items represent 50% of your inventory? If not, you may not have enough inventory for these items. Then calculate your inventory for each group. For the first chart, classify your items into A, B, C, and D (80%, 15%, 5%, 0%) based on sales. Gather sales and inventory in dollars by item. Any attempt to reduce inventory should be in harmony with this goal.

But remember, the overarching goal of the organization is to maximize long-term profits.

The key to sustainable reductions is to focus on the input variables. Here are 10 approaches to lowering your inventory. Some of this cost is based on the value of the product (cost of money, taxes, insurance, scrap) the rest is based on storage (warehouse space, maintenance, utilities, equipment). Generally it costs 20% to 40% of the materials cost or COGS per year to store. Inventory is usually a big number and in plain view to executive management and the shareholders. There’s no line item for supplier lead time, forecasting accuracy, or setup cost reductions. Too often, inventory is adjusted to meet financial goals, without corresponding improvements in the variables that drive inventory levels.īecause it shows up directly on monthly and quarterly financials. In order to achieve sustainable inventory reduction while maintaining or improving customer service, the variables that drive inventory must be improved. Inventory is a dependent variable based on the inputs of many factors including: demand and demand variability, supply lead time and lead time variability, supply chain design, manufacturing capabilities versus customer purchase characteristics, transportation modes, and desired service levels. Trying to control inventory independently of the variables that cause it is a no-win strategy. Because inventory reduction gets managed in a vacuum.
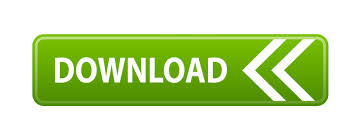